Craftsman Table Saw Miter Slot Tab Removal
4/5/2022 admin
Craftsman Table Saw Miter Slot Tab Removal Rating: 7,7/10 6722 reviews
Fits Craftsman table saw 315. Xxxxxx model miter gauges that use this type. Indicator- Part# 979978-001. Stop pin- Part# 979980-001. With the saw unplugged, mark 1 blade tooth. Raise the blade almost all the way. With the marked tooth at the forward position, use a tri square, and measure the distance from tooth tip, to miter slot. Move the blade, to the rear position and measure again. Table saw miter slot tab removal, SKILL SAW/CRAFTSMAN SAW - YouTube I used my die grinder with a cut off wheel to remove the tabs. Then I touched it up with a straight flat file. Check blade and table slot alignment. For clean, accurate crosscuts, a workpiece must travel parallel to the blade. Since most crosscutting depends on a miter gauge or other jig that rides in the table slots, it’s important that the slots and blade are parallel. Any deviation results in blade heel that can cause rough, out-of-square cuts.
Has your the cast iron top of the saw accumulated rust? Looking for the best way to remove the rust and stop it from rusting?
In fact, rust is one of the biggest threats to your table saw. Particularly cast-iron table is susceptible to rust in high-humidity climates.
Rust not only reduces its efficiency but also forces the user to choose costly maintenance. Rust is like cancer! It spreads gradually all over the surface. So, to stop it you must kill all of it!
But fear not.
This article on how to remove rust from table saw will help you a lot to do the work efficiently.
Believe me; you can do it quickly, and it’s much easier than you think!
How to Remove Rust from Table Saw- Step-By-Step Guidelines
- 400-grit wet-or-dry sandpaper/ synthetic kitchen scrubbing pad
- Dry, clean cloth/ paper towel
- Naval Jelly
- WD-40/ T-9/ Slipit/ Paste waxes/ paraffin waxes
- Hand gloves
Step 1: Assess the situation
The first thing you should do is assess the amount of rust on the table top. If there is only surface rust which is relatively light and minor pitting, then clean up won’t be very difficult.
On the other hand, if your unit has substantial and deep rust and major damage due to rust accumulating for several years if you have to work hard to remove it. On this situation, the surface may be still usable, but it won’t be as smooth of a surface when it was new.
Step 2: Remove the table saw accessories
It’s safe to remove the blade insert, blade itself, miter gauge and fence. You can also remove the rails.
Step 2: Have the PPE
Wearing a mask and eye protection is essential!
Step 3: Scour the surface
With 400-grit wet-or-dry sandpaper scour the whole surface. You may use synthetic kitchen scrubbing pad (not steel wool) to scour the top. Wipe off the surface with a dry, clean cloth or some paper towel to eliminate residual particles. Repeat this step as necessary.
If the rust is deep and heavier, you may use an orbital sander to help with the scrubbing to remove surface rust from cast iron table saw.
Step 4: Use Naval Jelly
Naval jelly is a gloopy, thick jelly made of Phosphoric acid. It is very effective to clean extremely rusted cast iron surface. It works quickly and does a good job for rust removing. This stuff is available at any local hardware store.
Before handling this product, wear hand gloves. Place the unit is a well-ventilated area. Open the door and set up a fan to ensure air moving to avoid breathing the nasty fumes from this chemical. Follow the instructions mentioned on the container.
Glob on or brush the naval jelly on the rusty top and spread it around. If you need to cover a large area, it’s convenient to use a paint sprayer to spray the stuff. Apply a thick layer and let it sit for 5 to 10 minutes. Then wipe it up along with the rust.
Apply more naval jelly to the pitted spots. Use some elbow grease and a rag to work into the pitted areas. You may also use a metal brush if you need to. The remaining rust will come up in no time.
When finished, you need to remove the residual acid properly. Rinse the surface with water soaked rag and dry it thoroughly.
To remove the rust from the table legs and hard to reach areas like the walls of the throat and miter slots, follow the step 3 and 4.
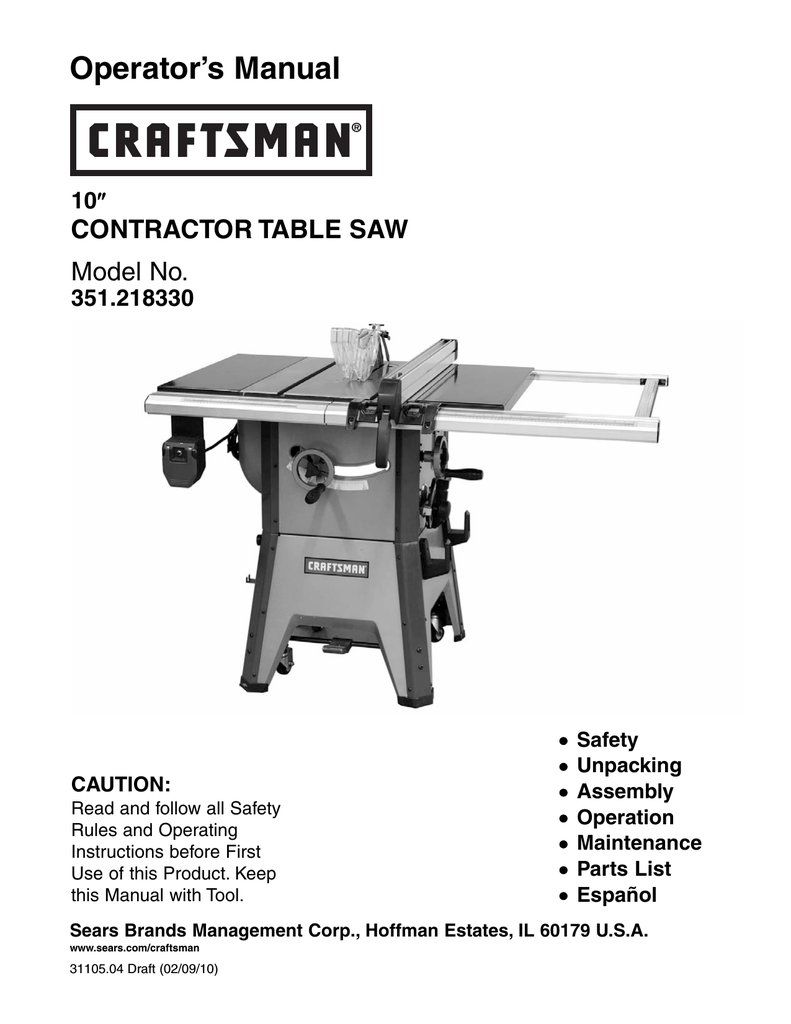
Removing Rust from Table Saw Blades
These steps should keep your table saw blades in top form.
- Wear rubber glove
- Lay the blades on a solid surface
- Apply penetrating oil over the top metal surface. Pay attention to the deep rusted areas.
- Scour the entire metal surface of the blade by using a steel wool pad.
- Apply more oil if needed.
- Wipe off the rust using a dry, clean rag.
- Follow the same procedure to remove the rust from the opposite side of the blade.
- Apply the wax on the blade. Follow the instruction mentioned on the wax container.
- Polish the wax from the blade. Apply a second layer of wax and re-polish the surface.
- Lubricate the blade after each use. Use WD-40, paste wax or gun oil before storing the blade.
Step 5: Protect the surface to prevent rust return
After removing the rust, it’s important to stop your table saw from rusting. Take the necessary measures to ensure that the rust won't return.
Several commercial products are available on the market to protect the cast-iron table from rusting. Some of these are:
- WD-40
- T-9
- Slipit
- Paste waxes/ paraffin waxes
These are available at your woodworking supplier or online.
# Protecting the surface from rust with WD-40 is effective if you store the machine for a cold winter. (The main purpose of WD-40 is removing water from metal tools and rust prevention)
Cover the dry surface with WD-40, and with a rag spread it thin. Use some more if necessary.
Note: If you’re planning not to use the table saw for a while, only use WD-4. But if you immediately use the unit after freshly lubricated, your workpiece may pick up the WD-40 which may cause a major issue when you’ll try to apply a finish to the wood.
# Alternatively, you can use paraffin wax or paste waxes to protect the surface of the table from rust. Apply the wax on the surface and let it dry for 15-20 minutes and then wipe off. Repeat the process at least one more time to make sure that all the surface area is covered with wax.
These waxes will not only protect the surface from rust but also smooth the surface so that your workpiece will glide easily across it.
Tips
Stay away from paste wax for cars. Many of these products contain silicone oil for water repellency and better shine which have negative impacts on the cast –iron. Paste wax for furniture or floors is also perfect to use.
Step 6: Reassemble the accessories
Back together everything. Insert the blade insert, reinstall your fence, etc.
After reinstalling all the accessories, your table saw is ready for service again. Have a look and admire the great job you’ve done!
Watch This: How Do You Clean a Rusty Table Saw Top?
Summing Up
Finally, the most important thing to do is avoid exposing your table saw to moisture. Although it’s quite difficult in the average workshop or garage, you should take measures to reduce exposure.
What’s more, avoid setting other tools or any drinks on the top of the table that may contain moisture.
Don’t forget to periodically apply a coat of wax on the table to prevent rusting.
If you can properly maintain your table saw, certainly, it’ll last for the life of the unit and serve you well.
Hope, this step-by-step guideline on the Best way to remove rust from table saw top has helped you a lot.
Now get to work and enjoy your woodworking!
This article is from Issue 45 of Woodcraft Magazine.
You only think your saw is working great.
Tuning up your tablesaw is one of the best steps you can take to becoming a better woodworker. You may think your saw is working just fine, but chances are it just isn’t performing as well as it could. Whether it’s an old saw or a new model fresh off the line, it probably has never been tuned up for premium performance. And tiny adjustments matter a lot when it comes to precision work.
Your saw’s table slots and fence may not be perfectly aligned to the blade path, causing rough or burned cuts. Blade angle stops that aren’t precisely dialed in can be causing less than perfectly square cuts. A misaligned splitter can lead to pinching or other feed problems, and stiff drive belts or poorly aligned pulleys could be causing vibration. These and other problems add up to a machine that’s not using its talents to its fullest.
Fortunately, it doesn’t take expensive tools or a lot of time to get your sawship shape. I’ll show you how to inspect, detect, and correct any shortcomings. I’m working on a cabinet saw in the photos, but most of the same principles apply to portable, contractor, and hybrid saws.
A precision straightedge and dead-on squares are must-haves for a successful tune-up.
The leaves on a feeler gauge allow precise measuring of tiny gaps.
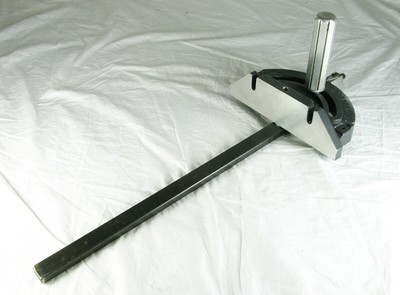
Tooling up
You probably already have most of the tune-up tools you’ll need, including a basic set of mechanic’s open-end wrenches, socket wrenches, Allen wrenches, and screwdrivers. You’ll also need a precision straightedge and an accurate square or two (Photo A). A 3' straightedge is perfect for our purposes here, but a 2' one (about $40) will work. A long, jointed piece of wood is okay for less precise measurements. A quality 4' engineers’ square will only set you back about $16, and art supply dealers sell plastic 45° drafting triangles for just a few bucks.
A feeler gauge (available at auto supply stores) is also useful (Photo B). Its thin metal leaves, gauged in thousandths of an inch, can be slipped into gaps to take precise measurements.
The only tool you may not have on hand is a dial indicator, and it’s well worth buying one for gauging the accuracy of many of your woodworking machines. (See sidebar on page 55.)
The tune-up sequence
There are certain tune-up steps that should be performed before others, depending on the type of saw you have and its condition. In general, approach the tune-up steps in the order presented here. I’ll note when deviations should be considered. Keep in mind that you may not need to make all of the following adjustments, as no fix may be required in some cases. However, make sure to check everything to determine where there might be problems.
Use a dial indicator to check the arbor flange for runout, which should be less than .001'.
Assess the arbor assembly
First check the integrity of the arbor assembly, which includes the arbor shaft, bearings, and pulley(s). Any slop in these parts can cause runout (wobble) in the arbor flange, which is a central tune-up reference point. If there’s a problem here (unlikely, except in well-worn older saws), there’s no point in continuing until it’s corrected because a wobbly flange will produce rough cuts even on an otherwise finely-tuned saw.
To check for slop, remove the drive belt(s) and try to move the arbor shaft up and down and in and out, listening and feeling for clunking noises or slop. Slowly spin the arbor, listening intently for grinding noises that might indicate worn bearings. Also try to spin and slide the pulley(s) while securely holding the arbor shaft. Any looseness here may indicate excessive wear that requires part replacement. The easiest fix for a faulty arbor assembly (again, unlikely), is to simply unbolt the entire arbor bracket (see your owner’s manual), and bring it to a machine shop for refurbishing.
Check the arbor flange for excessive runout, as any deviation here increases exponentially at the blade perimeter, causing rough cuts. Crank the blade carriage over to 45°, and scrub any crud from the flange with steel wool. Press the dial indicator plunger against the flange perimeter just enough to ensure contact throughout its rotation. Slowly rotate the arbor while monitoring the dial indicator (Photo C). The best saw manufacturers aim for less than .001' of runout. If you detect more, you’ll either have to live with it or replace the arbor.
Check the parallelism of the table slots to the blade using a dial indicator. Measure from the same spot on the blade, locating it both fore and aft.

Check blade and table slot alignment
For clean, accurate crosscuts, a workpiece must travel parallel to the blade. Since most crosscutting depends on a miter gauge or other jig that rides in the table slots, it’s important that the slots and blade are parallel. Any deviation results in blade heel that can cause rough, out-of-square cuts.
To best check the parallelism, screw a dial caliper to a scrap of wood that’s fastened to a snug-fitting runner in the table slot. I use a ZeroPlay guide bar, but a carefully fit wood strip will work, as long as there’s no sideways play. Fully raise your blade, and mark its plate near the perimeter. (The circular sticker in the photos is there only to provide better visibility.) Locate the mark near one end of the blade slot, lightly press the dial indicator against it, and zero-out the dial face (Photo D). Next, rotate the mark to the opposite end of the blade slot, and note the difference in measurement there to determine the amount of any non-parallelism (Photo E). (Rotating the blade like this eliminates any blade warp from the equation.)
No dial caliper? Use a feeler gauge to measure the distance between the blade and a screw in a stick of wood clamped to the miter gauge (left). If your miter gauge fits sloppily, attach the stick to a snug-fitting wood runner.
Lacking a dial caliper, you can go low-tech by driving a round-head screw into the end of a stick clamped to your miter gauge. Then use a feeler gauge to check the distance between the blade and screw, again measuring fore and aft of the blade slot (Photo F).
If your miter gauge bar fits sloppily, glue the stick to a snug-fitting wooden runner (Photo G).
If the parallelism is out more than .003', I recommend a realignment. (Note: With a cabinet saw, realignment is best done after cleaning the internal mechanisms, for which you’ll want to remove the saw top.) To align a contractor’s saw or portable saw, you’ll need to shift the position of the arc-shaped trunnion brackets, which bolt the entire saw carriage to the underside of the table. Loosen all four trunnion bolts, leaving one of the front bolts snug (but not tight) to serve as your pivot point. Next, use a soft-faced mallet to tap the rear trunnion bracket right or left as necessary to align the blade to the table slots.
On a cabinet saw, it’s easier. Simply loosen the four bolts that attach the saw table to the corners of the cabinet; then shift the table as necessary by tapping it at the edge with a mallet, as shown in the photo on page 52. Monitor your progress with a dial caliper.
When retightening the bolts, snug them up gradually in turn, as fully tightening one at a time risks shifting the trunnions or tabletop. Recheck the parallelism afterward.
Dial Indicators
For checking the accuracy of your tablesaw and other machines, it’s hard to beat a dial indicator. It consists of a spring-loaded plunger whose movement is indicated in thousandths of an inch on the face of a dial. You can use it to determine the concentricity of shafts, flanges, blades, and chucks, as well as the projection and travel of knives and other cutters.
To use the tool, secure it next to the part to be measured. A lug on the back allows attachment to an adjustable boom arm on a magnetic base (for convenience on ferrous metal surfaces.) Alternatively, you can screw through the lug hole into an appropriately sized piece of wood that’s clamped in place.
You don’t need an expensive dial indicator to measure most woodworking equipment. You can get a perfectly acceptable indicator and magnetic base for about $40.
Clean gear teeth with a toothbrush, continuously dipping it in mineral spirits as you work.
Craftsman Table Saw Miter Track
Crank the motor carriage fully over both ways to best access the trunnion grooves.
Clean the internal mechanisms
For smooth operation, your saw’s pivot points, trunnion brackets, and gears need to be cleaned, lubricated, and kept free of oily sawdust that can gum up the works.
To familiarize yourself with the internals of your particular saw, refer to your machine manual. Don’t have it? Some manufacturers offer them online. Or simply scrutinize your saw. If you’re mechanically inclined at all, everything you need to see will be very apparent.
You can easily access the internals on a portable saw or contractors’ saw by turning it upside down on a bench. With a cabinet saw, the best approach is to remove the table. However, if the table is already well aligned to the saw blade, you may not want to remove it, especially if you have already built slot-traveling jigs that might then be thrown out of adjustment. Instead, work through the cabinet door, perhaps temporarily removing the motor for better access to the blade carriage and other parts.
Blast the interior with compressed air, and then use mineral spirits to clean away any crud and grease. Use a stiff-bristle toothbrush–continuously dipping it in the spirits–to clean gear teeth (Photo H) and other complicated parts. To expose the trunnion bracket grooves, fully crank the blade carriage over one way, and then the other (Photo I).
Lubricate the gears and trunnion grooves using a non-greasy, rust-protectant aerosol spray.
Lubricate all moving parts. Don’t use oil or grease on the gears or trunnions, as it attracts sawdust. Instead, spray them with a silicone-based lubricant (Photo J). Alternatively, you could apply a thin coat of paste wax, using a clean toothbrush for gear teeth and the like. To lubricate the arbor shaft, hand wheel shaft, and other pivoting points, use a thin penetrating oil like WD-40. Avoid getting lubricant on the belts or pulleys.
Eliminate vibration
A saw should stand solidly with no rocking, and be free of vibration in use. Rocking–usually caused by an uneven shop floor–can be corrected by shimming the saw feet. Working vibration is often caused by pulley misalignment, which can be corrected with the use of a straightedge held against the pulleys while adjusting them into the same plane. The stock die-cast pulleys on many contractors’ saws can also cause vibration due to non-concentricity. These can be replaced with machined steel pulleys.
“Belt slap”–caused by a rubber drive belt’s “memory” of its oblong packaged shape–can also cause working vibration. Replacing rubber belts with “link” belts eliminates this problem (Photo K). To tension a belt on a cabinet saw, pivot and lock the motor on its mount so that the belt deflects about 1' at its center point, as shown in Figure 1.
Vibration-free link belts can be sized to replace stiffened rubber V-belts that tend to gallop on their pulleys.
A jointed stick serves as a straightedge for aligning the saw table and extension wings.
Adjust the Allen screws in a stock throat plate to bring it level to the table.
Level the top
Check the level of the extension tables (or “wings”) using a long, jointed stick as a straightedge (Photo L). First flush up the wings to the main table. On a typical contractor’s saw, the extensions are bolted to both the saw table and the fence rails. If necessary, loosen the bolts, level the extension, and then retighten the bolts.
The cast-iron extensions on cabinet saws are typically bolted only to the main table. If an extension droops at its outer end, raise it by inserting paper, plastic, or aluminum shims at the underside of the joint. If the outer edge of the wing is too high, insert the shims at the topside of the joint. Finally, adjust the height of your throat plate using its leveling screws, with a short straightedge spanning the plate opening (Photo M).
When this cabinet saw blade carriage is cranked over to 45°, the stop bolt pivots up against a raised nub.
Gauge the blade angle with a drafting triangle, and adjust the saw carriage stops to suit.
Adjust the blade stops
Stops for setting the blade at 90° and 45° typically consist of an internal adjustable bolt that is locked in position with a jam nut (Photo N). Refer to your saw manual for the location of the stops, or just peer inside the saw while cranking the carriage over.
Table Saw Miter Slot Size
Check the blade at 90° and 45° in turn, with the blade carriage cranked completely against each stop without excessive pressure. A plastic 45° drafting triangle is perfect for the job (Photo O). Adjust each stop as necessary.
Follow up by taking a few test crosscuts and miter cuts on thick, narrow sticks of straight, dressed stock, trimming off at least 1⁄4' to prevent blade deflection. (Lacking an accurate miter square, you can place two mitered test cuts together against a good try square to check for a tight joint at 90°.) If the test cuts don’t prove accurate, readjust the stops. When they’re set correctly, tighten the jam nut on each, and repeat the test cut procedure.
Align a splitter or riving knife with the edge of the teeth facing the saw fence.
Having aligned the table slots to the blade, use a dial indicator to align the fence to the slots.
Align the splitter
A properly aligned splitter or riving knife is crucial for preventing kickback, which is the primary cause of tablesaw accidents. Place an accurate straightedge against the right-hand face of the teeth (not the blade plate); then align the splitter or riving knife to the straightedge (Photo P). Use a small square to ensure that the splitter is also square to the tabletop.
Adjust the fence and miter gauge
For safe, clean cuts, the rip fence must be adjusted parallel to the blade. Because you have already adjusted the table slots to the blade, you can now adjust the fore and aft ends of the fence to the slots, as shown in Photo Q. Most importantly, make sure that the aft end of the fence doesn’t angle inward toward the blade, which invites pinching and kickback. Some woodworkers angle the aft end away by 1⁄32' or so for a measure of safety.
Some fences include alignment screws for adjusting vertical fence tilt.
A drafting triangle works well for setting the 90° and 45° stops on the miter gauge.
The fence faces should also be adjusted square to the table. Some fences include adjustment screws in the crossbar to correct tilt (Photo R). Without them, adjusting a tilted fence generally requires shimming between the faces and the fence body. (For metal-faced fences, you may need to attach a shop-made facing.)
For accurate crosscutting using a miter gauge, its bar must fit snugly in the table slots without sideways play. The miter gauge head must also be aligned perfectly square to the blade. The time-honored low-tech trick to correct the fit of a loose bar is to dimple its edges with a metal punch to expand the metal a bit. If aggressive pounding causes the bar to then stick in its slot, file the edges of the bar down a bit.
Once the bar fits well, use a drafting triangle to set the miter gauge head square to the blade (Photo S). Then adjust the 90° stop on the miter gauge head. Also use the triangle to set the 45° stops.
Cleaning and protecting surfaces
Clean the saw table and fence rails with mineral spirits. Scrub away light rust using fine steel wool lubricated with mineral spirits. For heavier rust, use the finest grit possible of silicon carbide wet/dry paper, again lubricated with mineral spirits.
Wipe away the spirits. Wax the table top, the rails, and areas where the fence contacts them. Also wax the faces of the fence, buffing the wax well with a soft, clean cloth. While various metal protectant sprays seem to work fine, I’ve not found them to be any better than paste wax.
About Our Author
Table Saw Miter Slot Rails
Senior editor Paul Anthony is the author of Taunton’s Complete Illustrated Guide to Tablesaws, from which this article is excerpted.